LPG Cylinder and Propane Tank Production Line
LPG cylinder production line, also named as Propane tank production line, LPG Gas Cylinder Production Line, which has now become the growing business in Southern-East Asia, South America and Africa. THLPG undertakes project design, manufacture and installation of turnkey plants for all types and sizes of Steel LPG Cylinders, Automotive Gas Tanks, LPG Cylinder Valves, especially in compliance with all relevant international standards such as EN, DOT, BS, KS etc. No need huge investments, we can help you fulfill your business dream and start production!
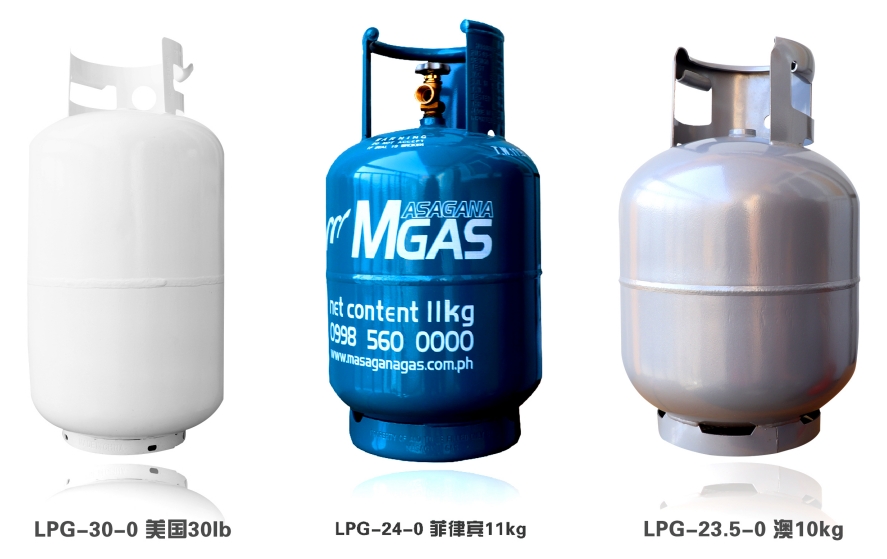
Production Line Specification
The Reasons to Choose THLPG:
We are a manufacturer of all LPG cylinder / Propane cylinder making machinery with more than 26 years of experience, such as Guard Ring Production Line, Foot Ring Production Line, automatic polishing trimming & joggling machines, inside and outside bung welding machines, inside and outside foot ring welding machines, inside and outside guard ring welding machines, automatic propane cylinder furnace, automatic hydraulic pressure testing machine, automatic LPG cylinder tare weighing machine, automatic air leakage testing machine, automatic LPG cylinder blanking machine, automatic LPG cylinder plastic foaming machine, automatic LPG gas cylinder screen printing machine etc and other LPG gas cylinder making machine, other gas cylinder welding line and other LPG Production Line Machinery. With advanced technology and best service, we have cooperated with many clients from all over the markets like Philippines, Malaysia, Bangladesh, Vietnam, Turkey, Colombia, India, Venezuela etc.
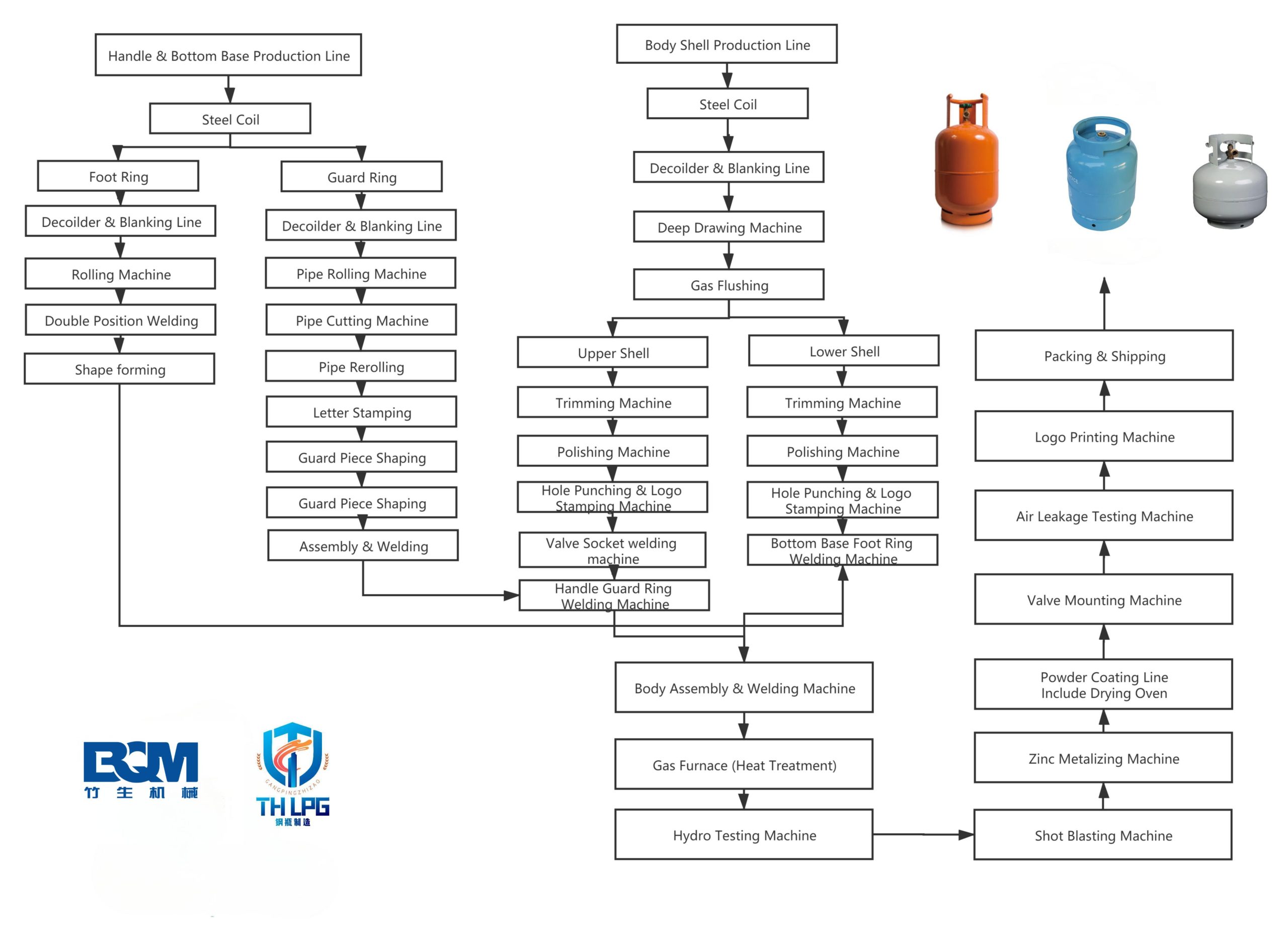
LPG Cylinder Body Blanking and Forming Line
The steel coils are cut to the required size by hydraulic blanking machines or mechanical punching machines. The steel coil blanks are manually/automatically loaded into a specific hydraulic deep drawing press to form the upper and lower halves of the LPG cylinders. The deep drawn parts are then trimmed and meshed on a trimming and meshing machine before welding so that the upper and lower parts match when assembled together.
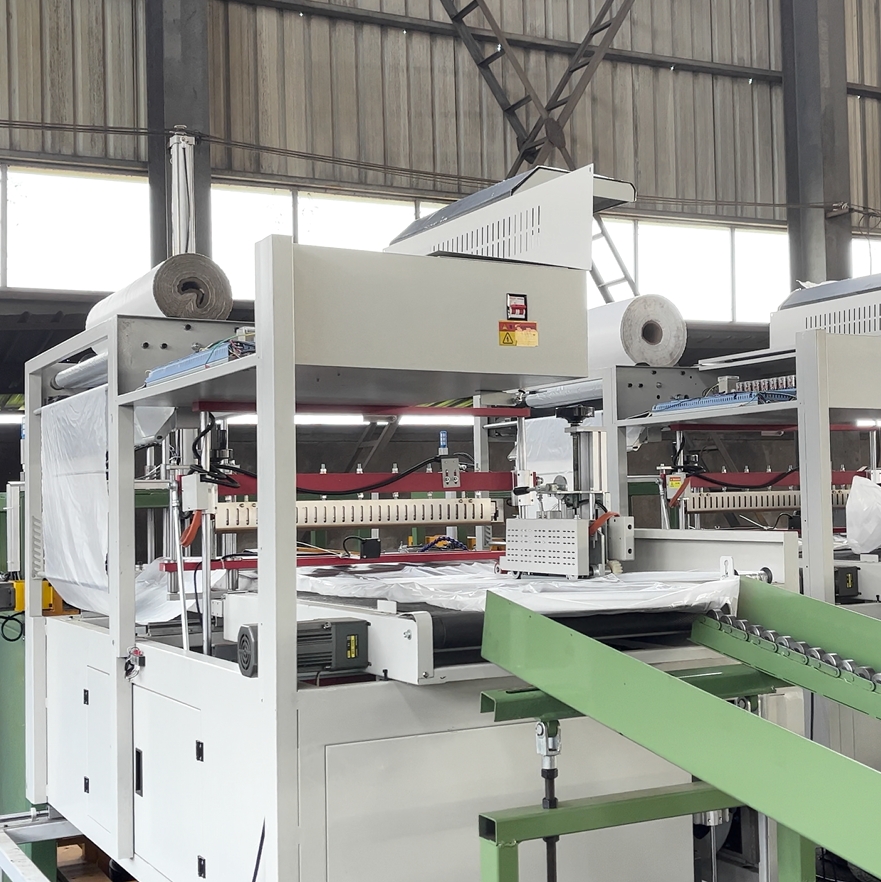
Plastic Film Covering Machine
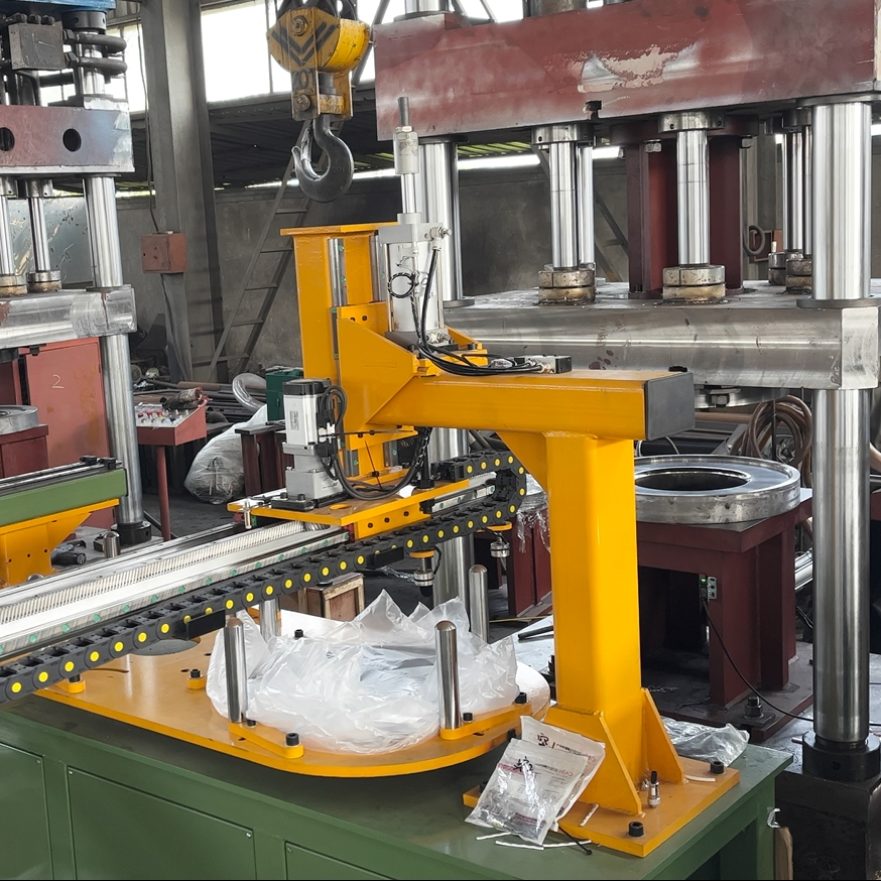
Deep Drawing Hydraulic Press with Conveying Sets
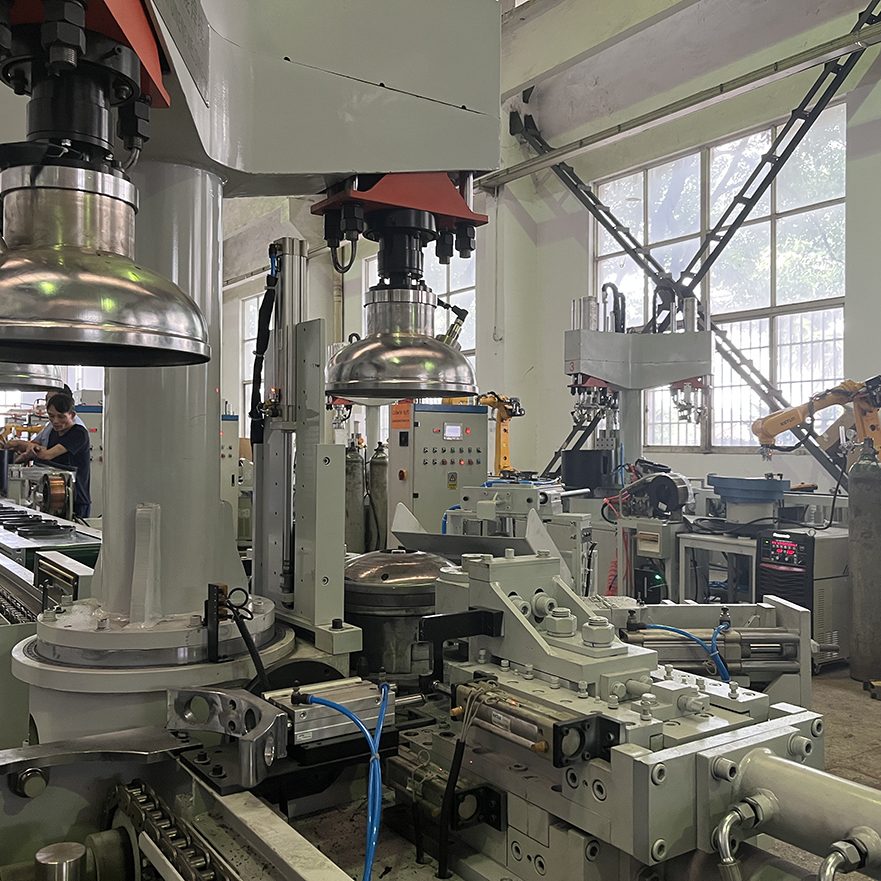
Trimming and Joggling Machine
LPG Cylinder Foot Ring and Guard Ring Production Line
The compatible production line can produce various types and sizes of retaining rings and foot rings. The production line is designed and produced by “THLPG”. It mainly consists of unwinding machine, straightening machine, feeder, blanking machine, mechanical punching machine and related tooling, automatic tube bending machine, serial number embossing machine and various welding machines.
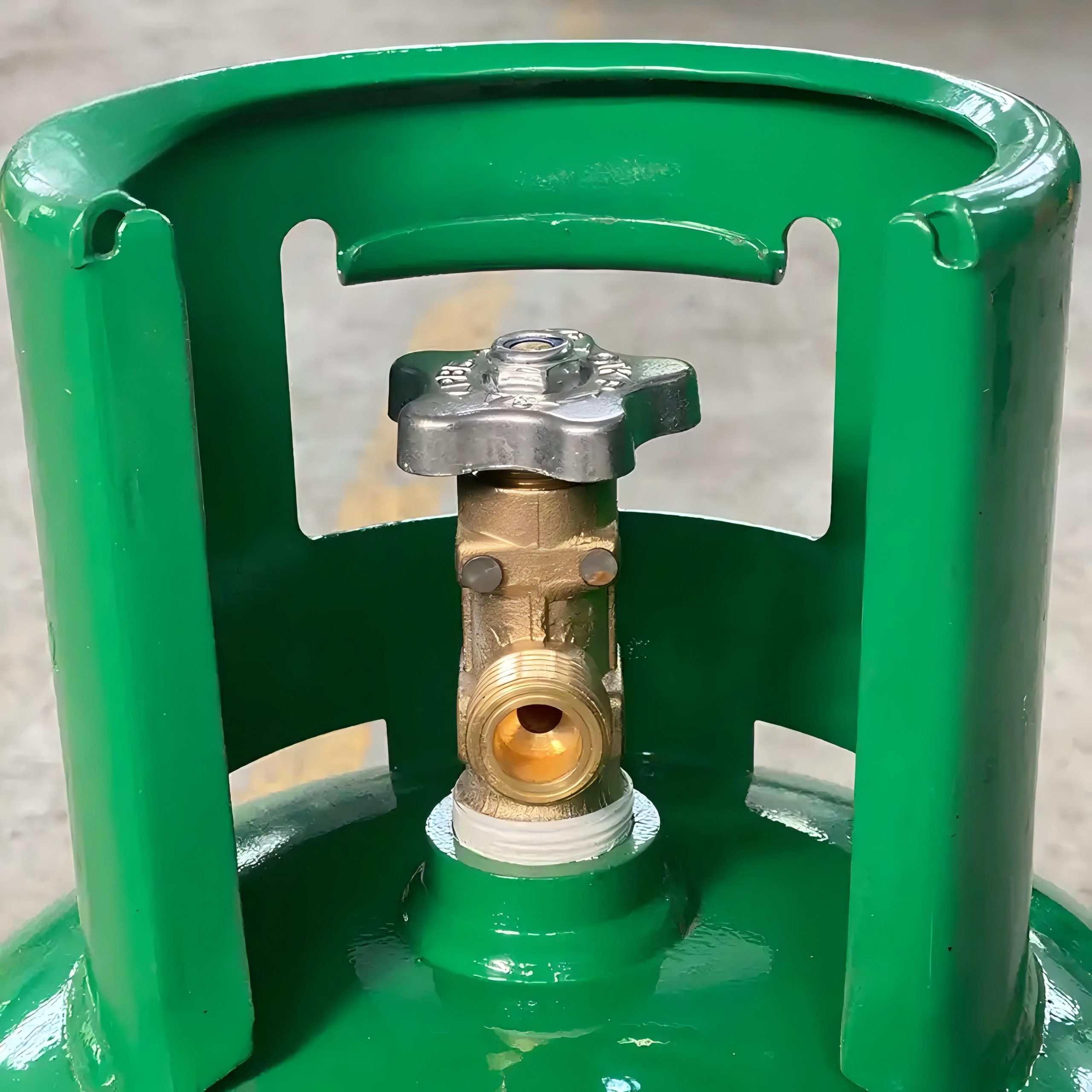
Guard (Collar) Ring
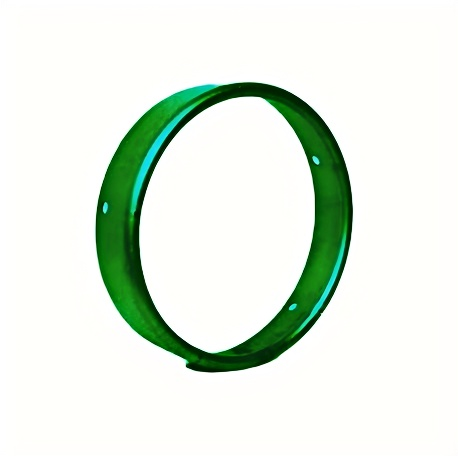
Foot Ring
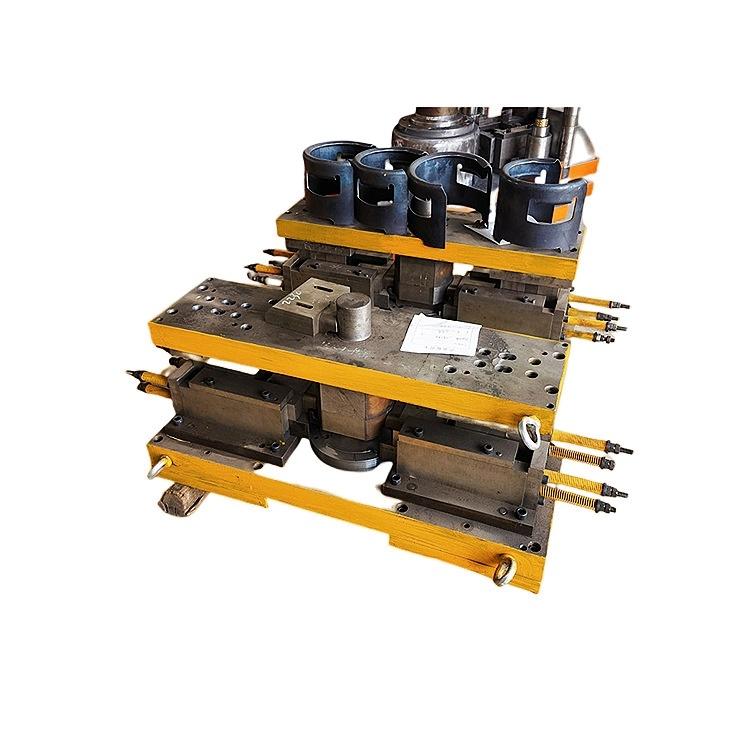
Presses & Tool Sets For Blanking Stamping Forming
LPG Cylinder Body Welding Line
Guard Ring and Foot Ring are welded to the upper and lower half of the bottle body by an automatic welding machine. Bung is welded to the upper half of the bottle body. Then the upper and lower half of the bottle body will be welded together by an automatic ring welding machine. Three-piece liquefied petroleum gas cylinders are welded by special automatic longitudinal and ring welding machines. The most popular welding technology at present is MIG welding, which is economical and fast, thus greatly increasing production capacity. If local special gases are scarce, submerged arc welding technology can also be used.
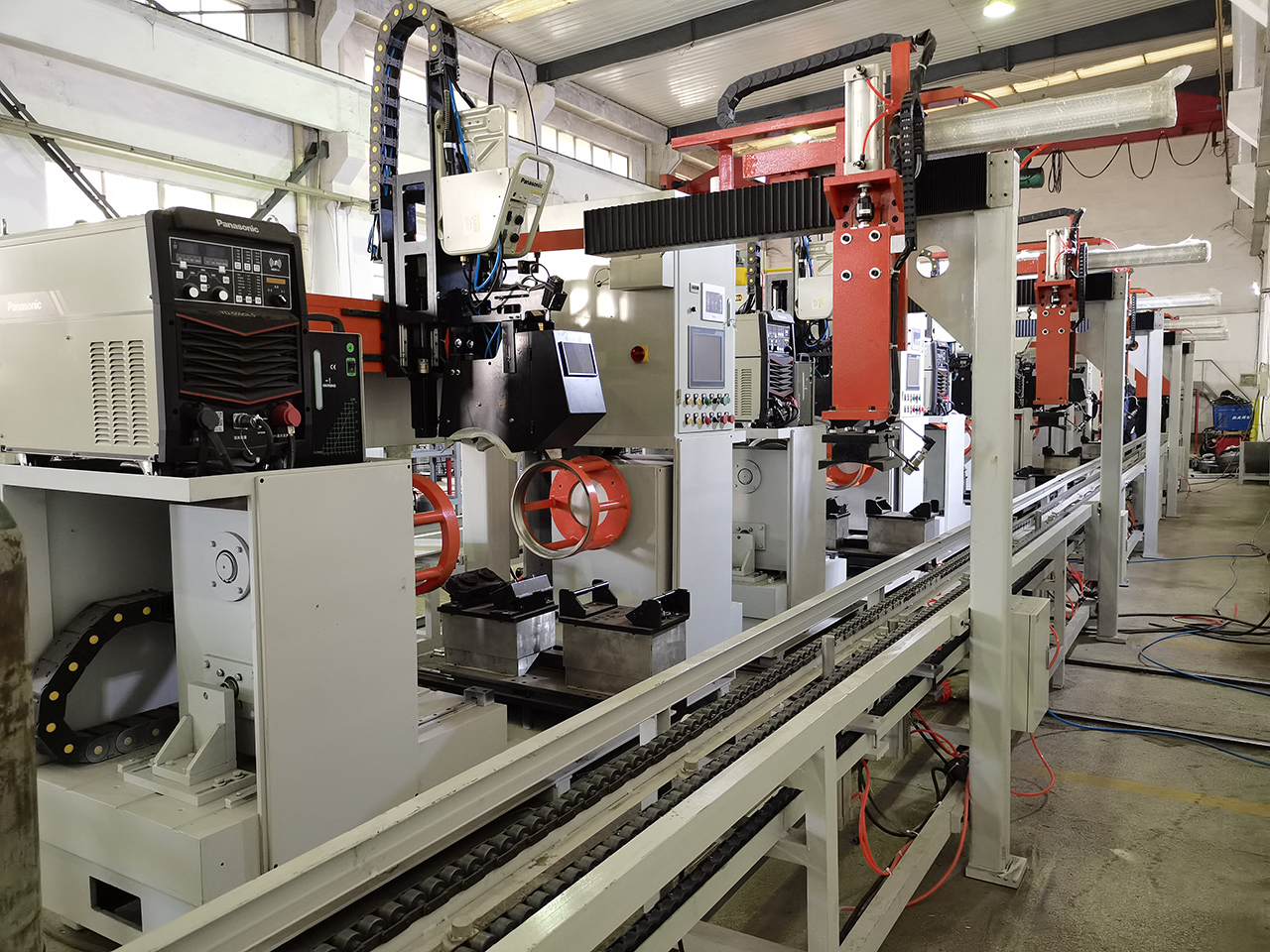
LPG Cylinder Body Longitudinal Seam Welding Machine
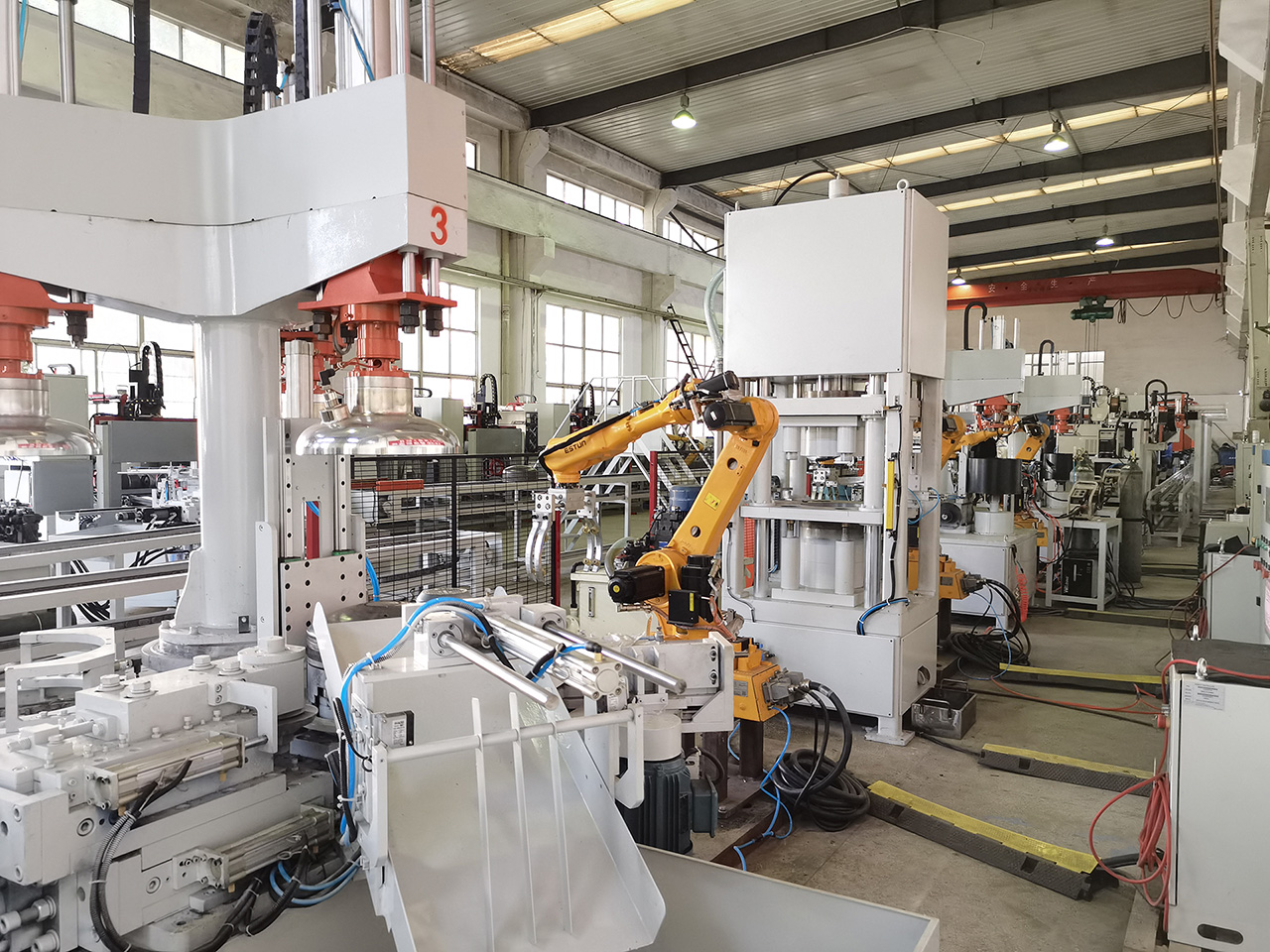
LPG Cylinder Guard Ring & Foot Ring Welding Machine
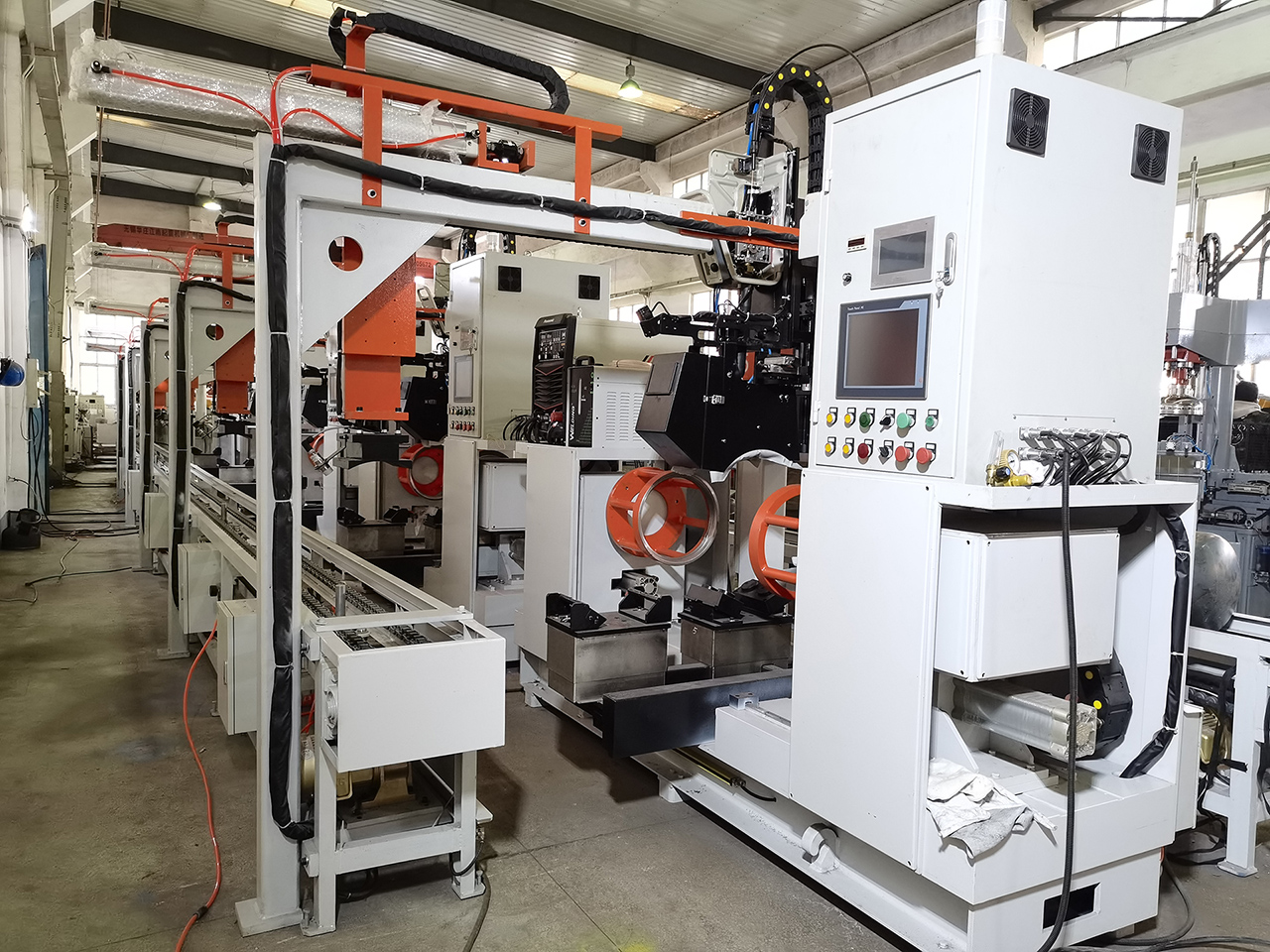
LPG Cylinder Body Circumferential Seam Welding Machine
LPG Cylinder Heat Treatment & Hydrostatic Testing Line
All welded LPG cylinders and auto gas tanks are normalized after the deep drawing and welding process. A conveyor system transports the cylinders from the inlet through a high-tech oven to the outlet where they go through preheating, heating and cooling stages before entering the appropriate heat treatment stage. All cylinders are heated to 930°C and held at that temperature for a certain period of time.
After the heat treatment process, all cylinders are gradually cooled and then hydrostatically tested at 34 bar pressure to visually check for forming and welding defects. On request, we can provide a fully automatic in-line hydrostatic testing machine to reduce your workload and increase your production efficiency.
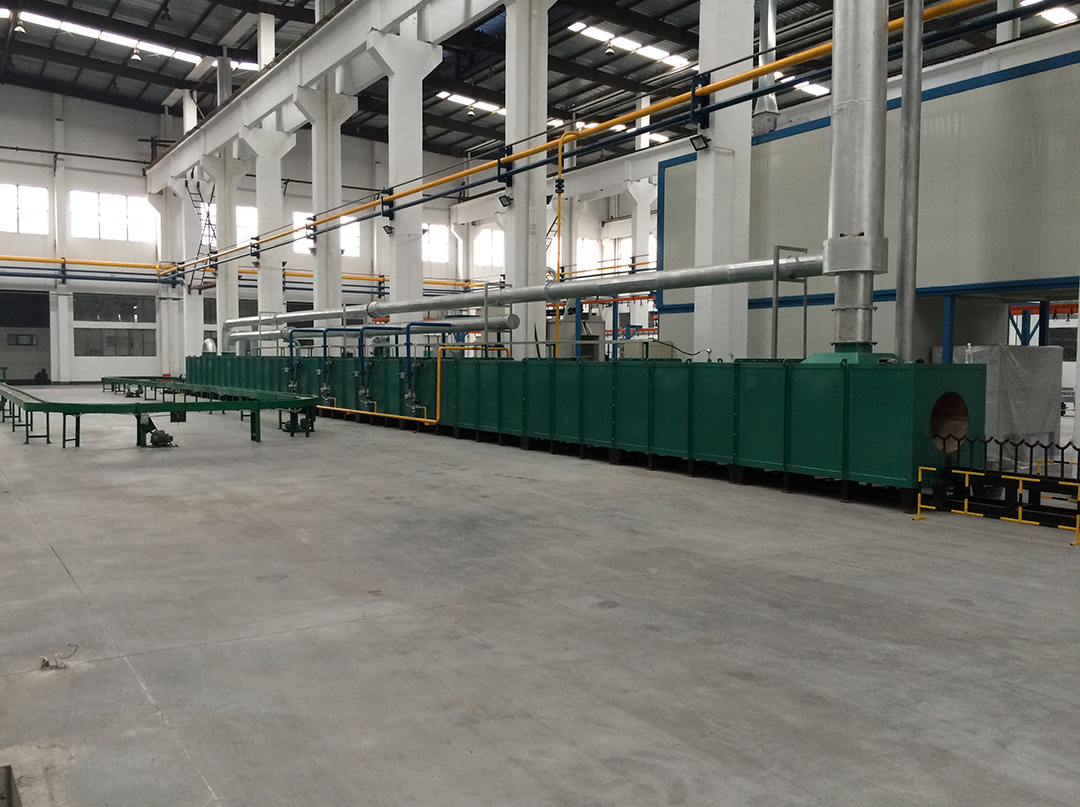
Normalizing Furnace With Roller Conveyor
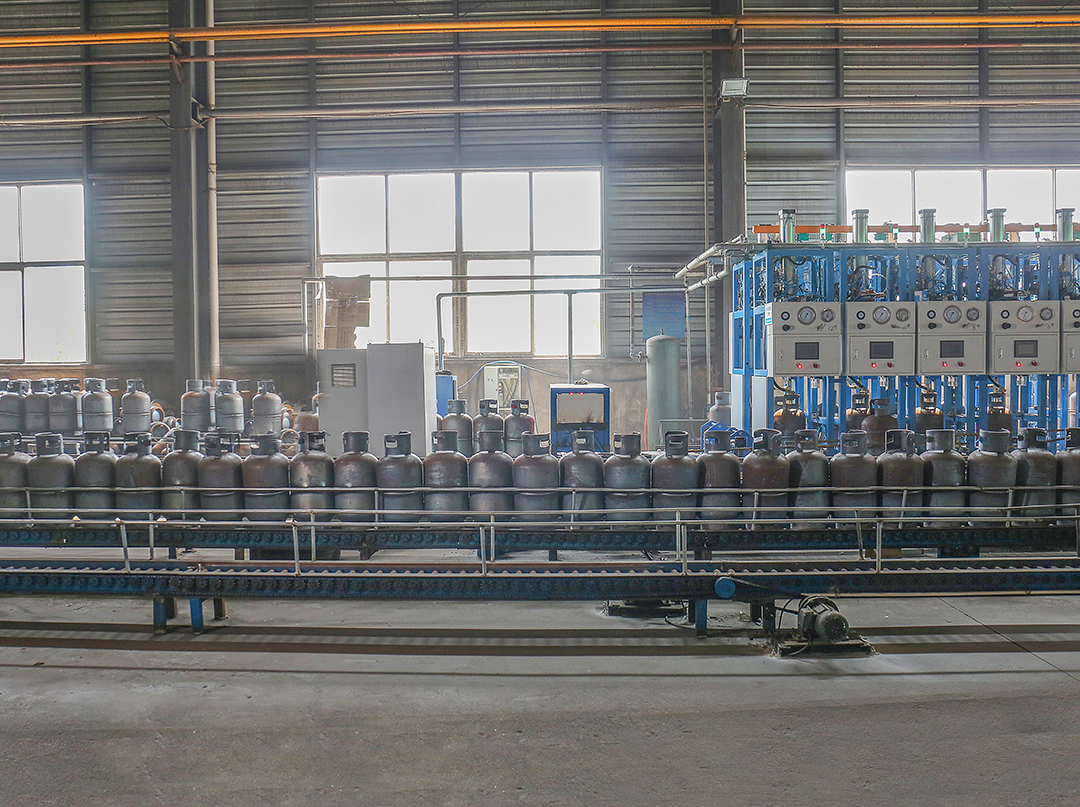
Hydrostatic Testing Machine
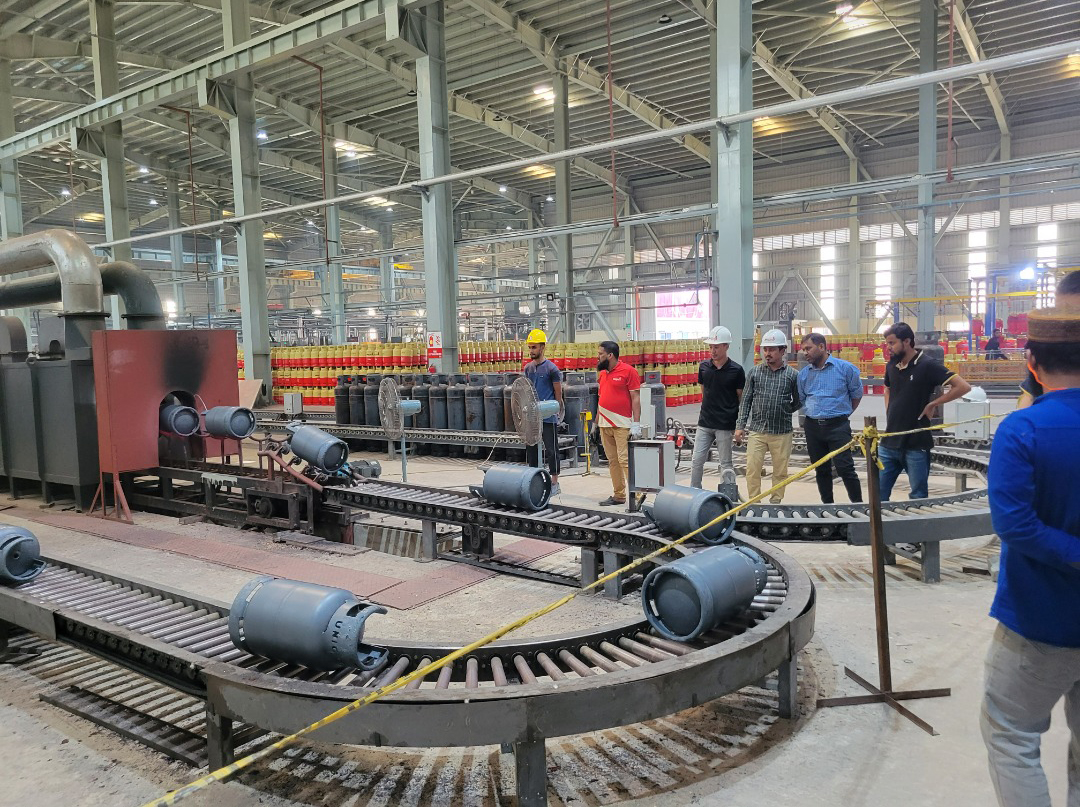
Normalizing Furnace With Roller Conveyor
LPG Cylinder Surface Treatment Line: Shot Blasting, Zinc Metallization and Liquid Painting / Powder Coating
After heat treatment, LPG cylinders are shot blasted to remove any rust and better prepare for zinc and painting. LPG cylinders are galvanized using an automatic arc spray metallizing gun and automatically sprayed using electrostatic powder spraying method by spray gun and cured in a tunnel paint curing oven. If requested, a second wet paint can be applied on the same line.
The cylinders can be automatically loaded and unloaded onto the shot blasting machine and the painting line conveyor chain using a simple automatic leveling device developed and produced by us.
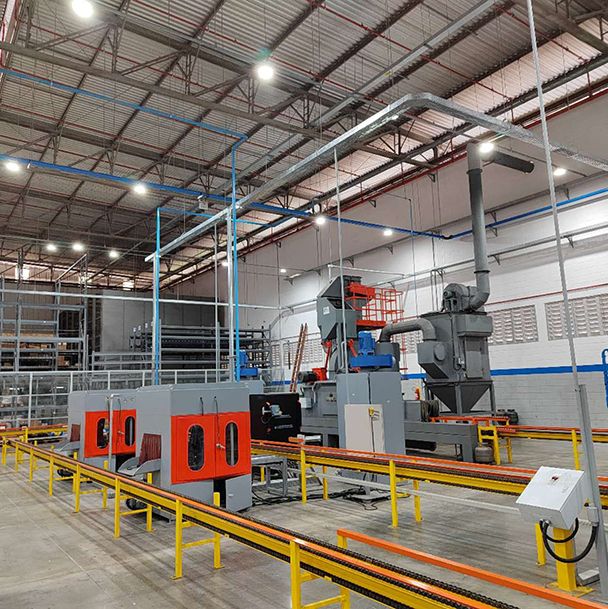
Shot Blasting Machine and Zinc Metallization Machine
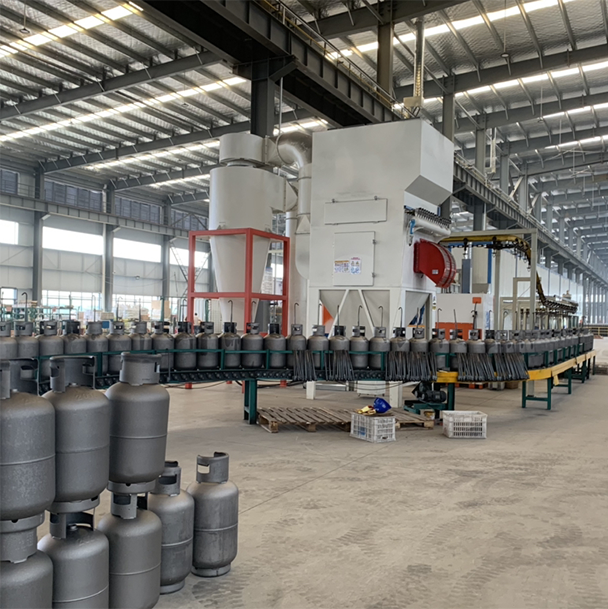
Shot Blasting Machine
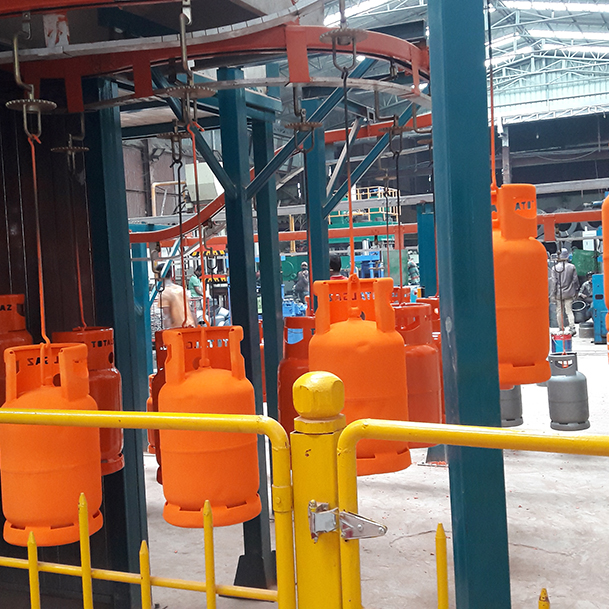
Powder Coating Line
LPG Cylinder Finishing & Air Leakage Testing & Logo Printing Line
Net weight weighing, inline logo printing, valve thread cleaning, valve tightening, leak testing, vacuuming, laser marking, QR code installation and other processes are all automatically completed on the online finishing and leak testing line.
Single-color logos and labels are printed by screen printers, and multi-color logos are printed by automatic pad printers. Currently, many countries require QR codes to be attached to cylinders for subsequent safety management and traceability. China’s GB standard requires welding on the cylinder guard ring, and some countries allow rivets to be riveted on the guard ring.
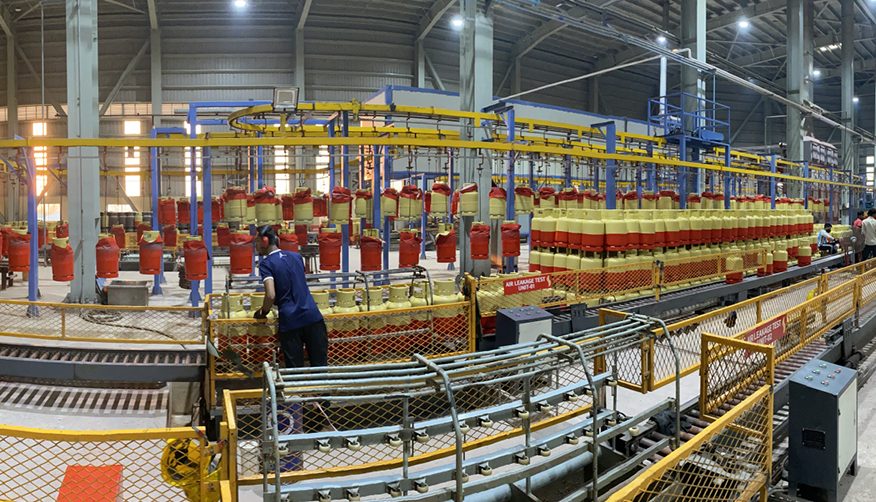
Air Leakage Testing Machine
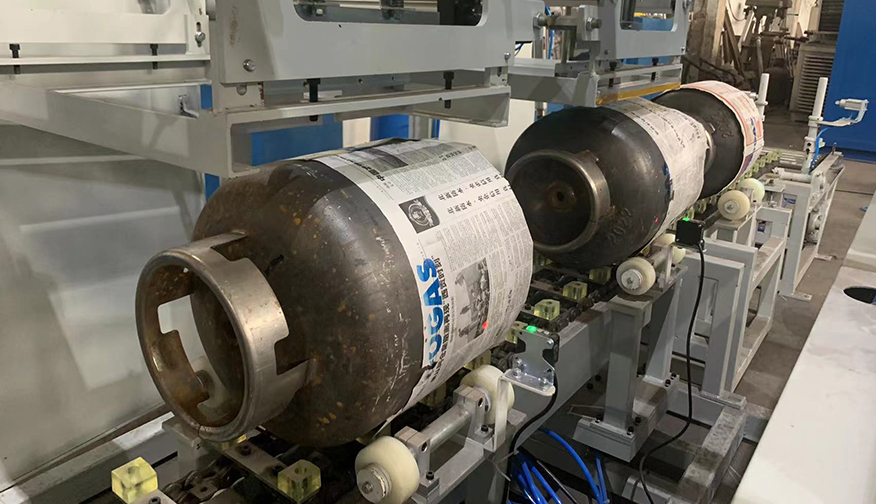
Silk Printing Machine
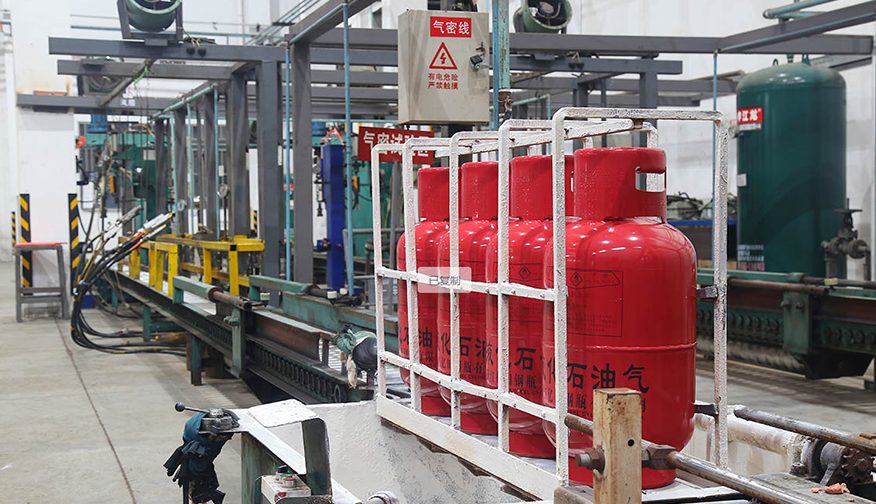
Tare Weighing and Vacuum Line
Testing Equipment for LPG Cylinder Production Plant
Some major testing machines for LPG gas cylinder production. Based on specific regulations, there will be different testing standards & machines required.
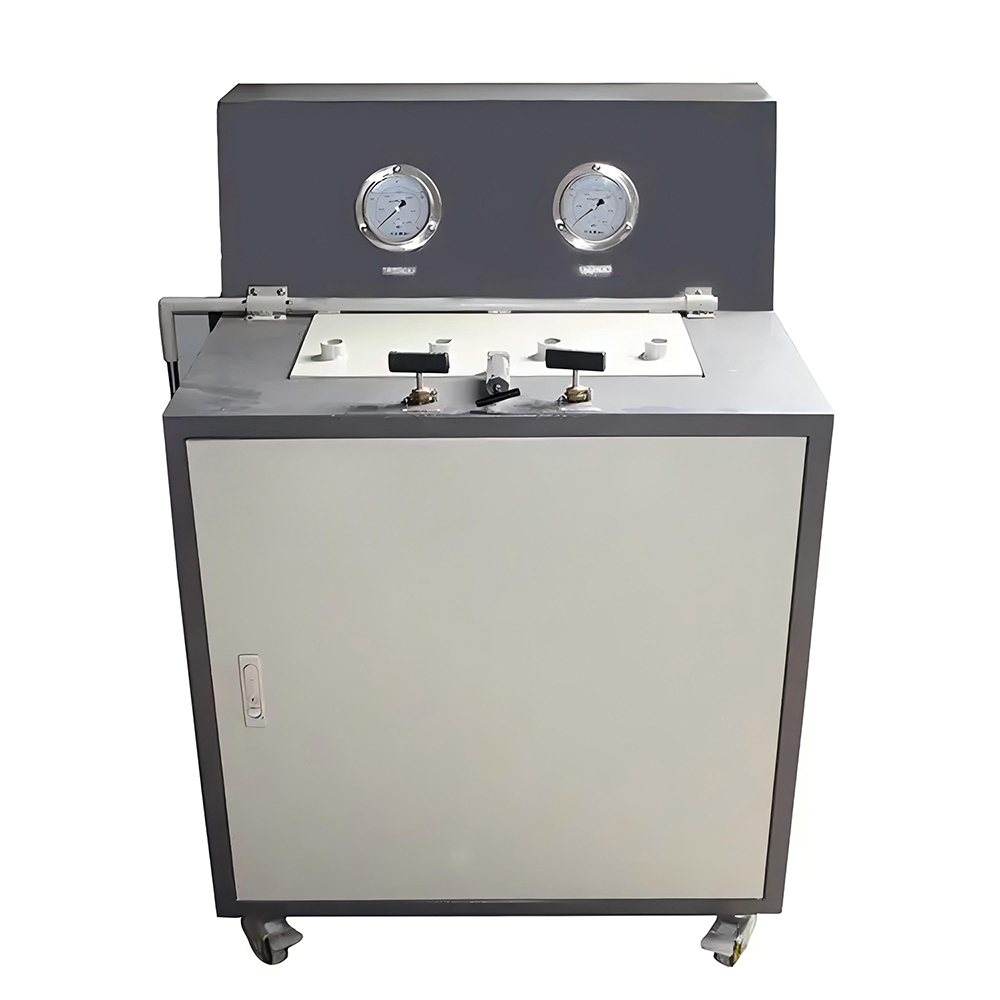
LPG Valve Testing Machine
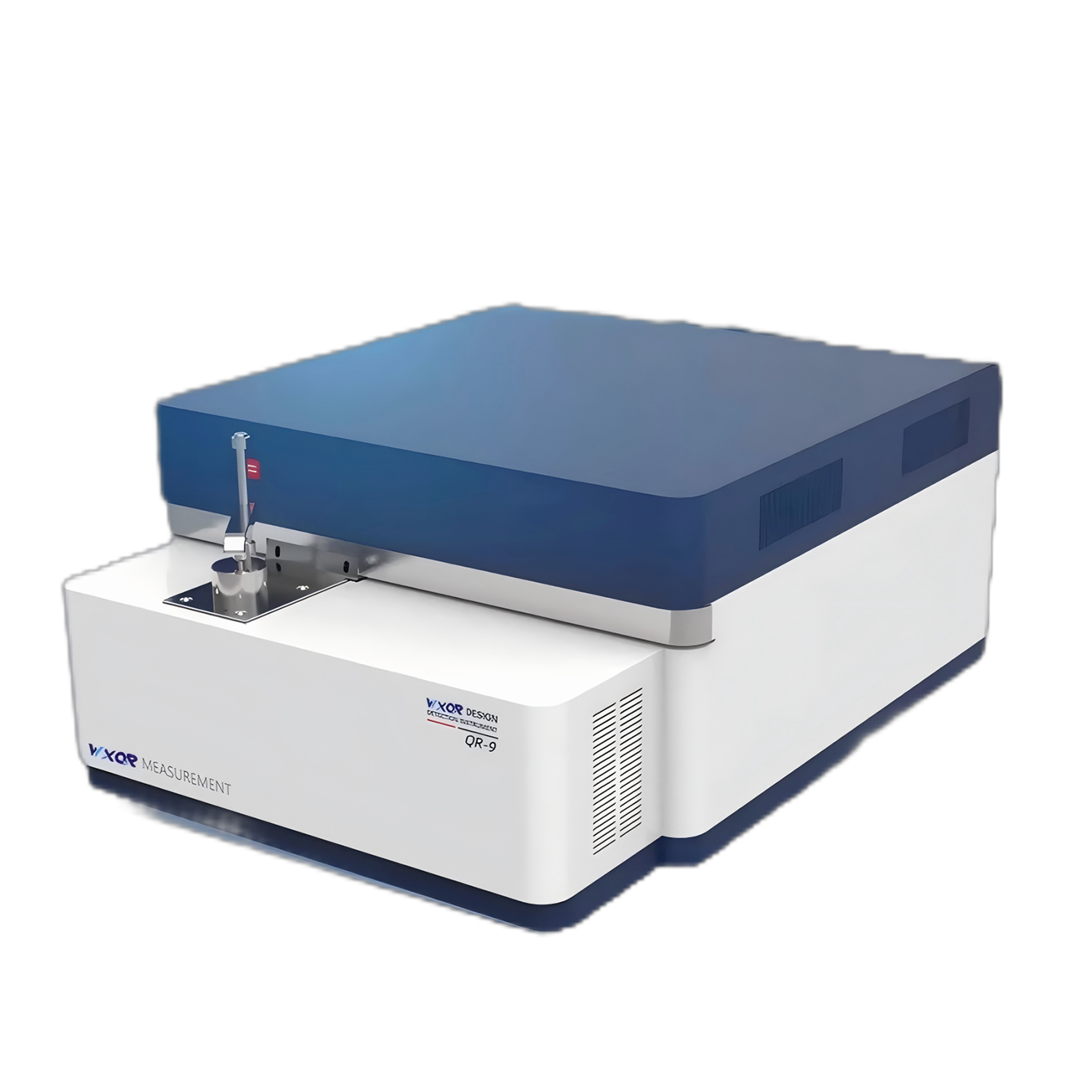
Spectrometer
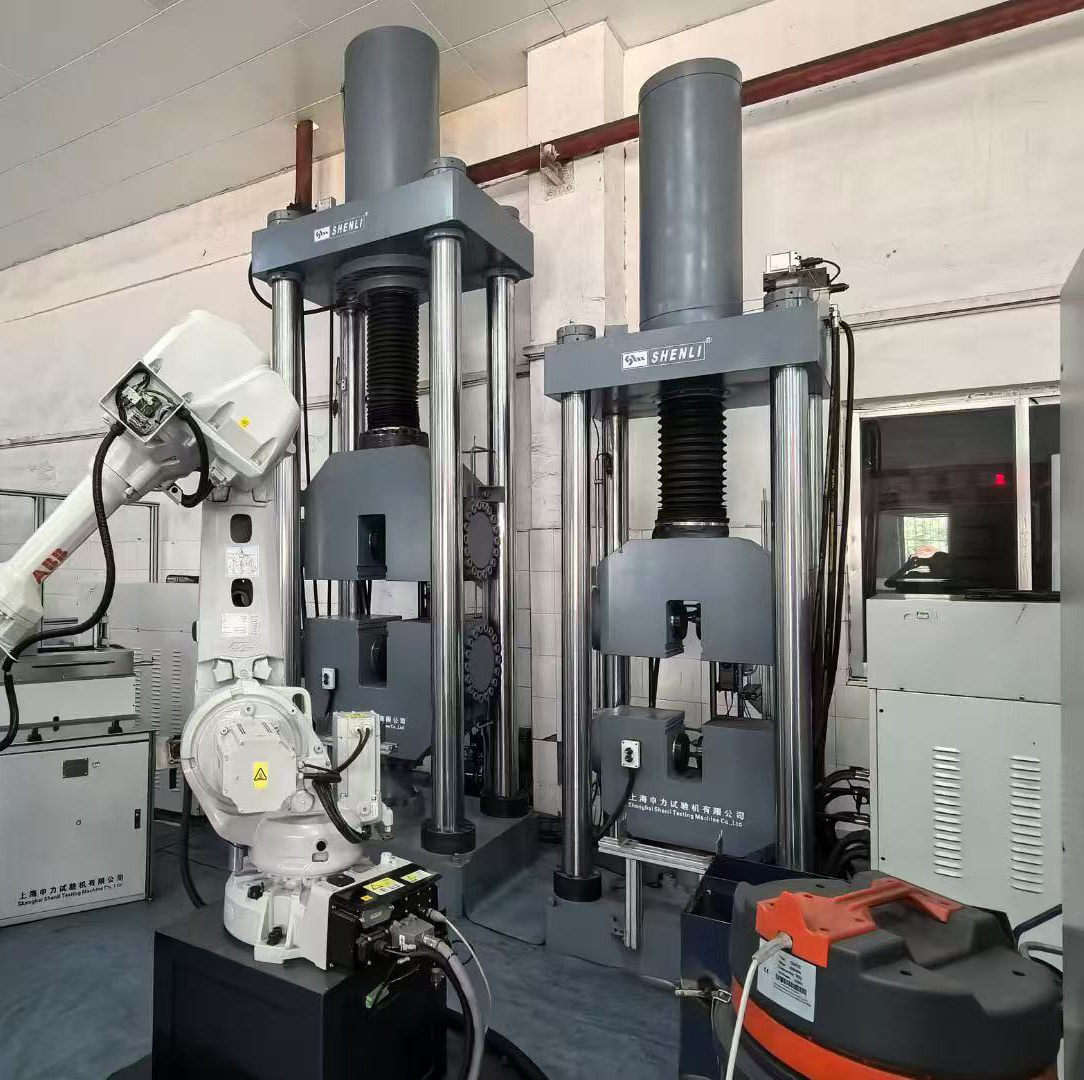
Tensile and Bending Testing Machine
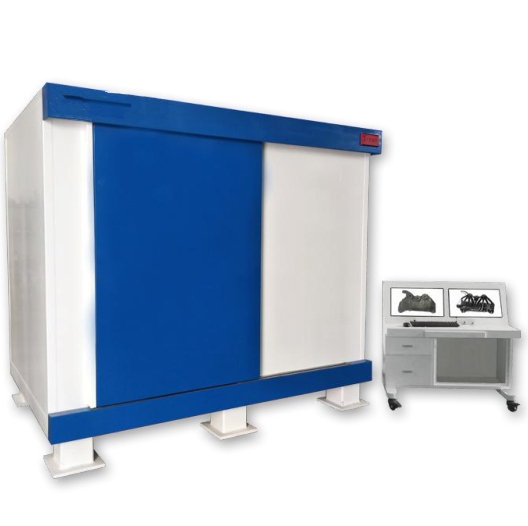
Inline X-Ray Testing Booth
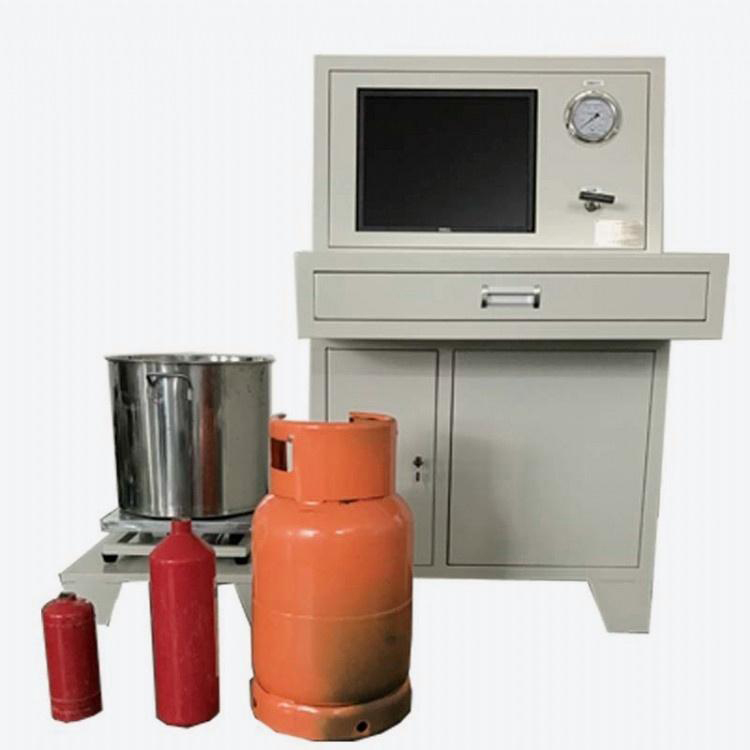
Burst Test and Aging Test Machine
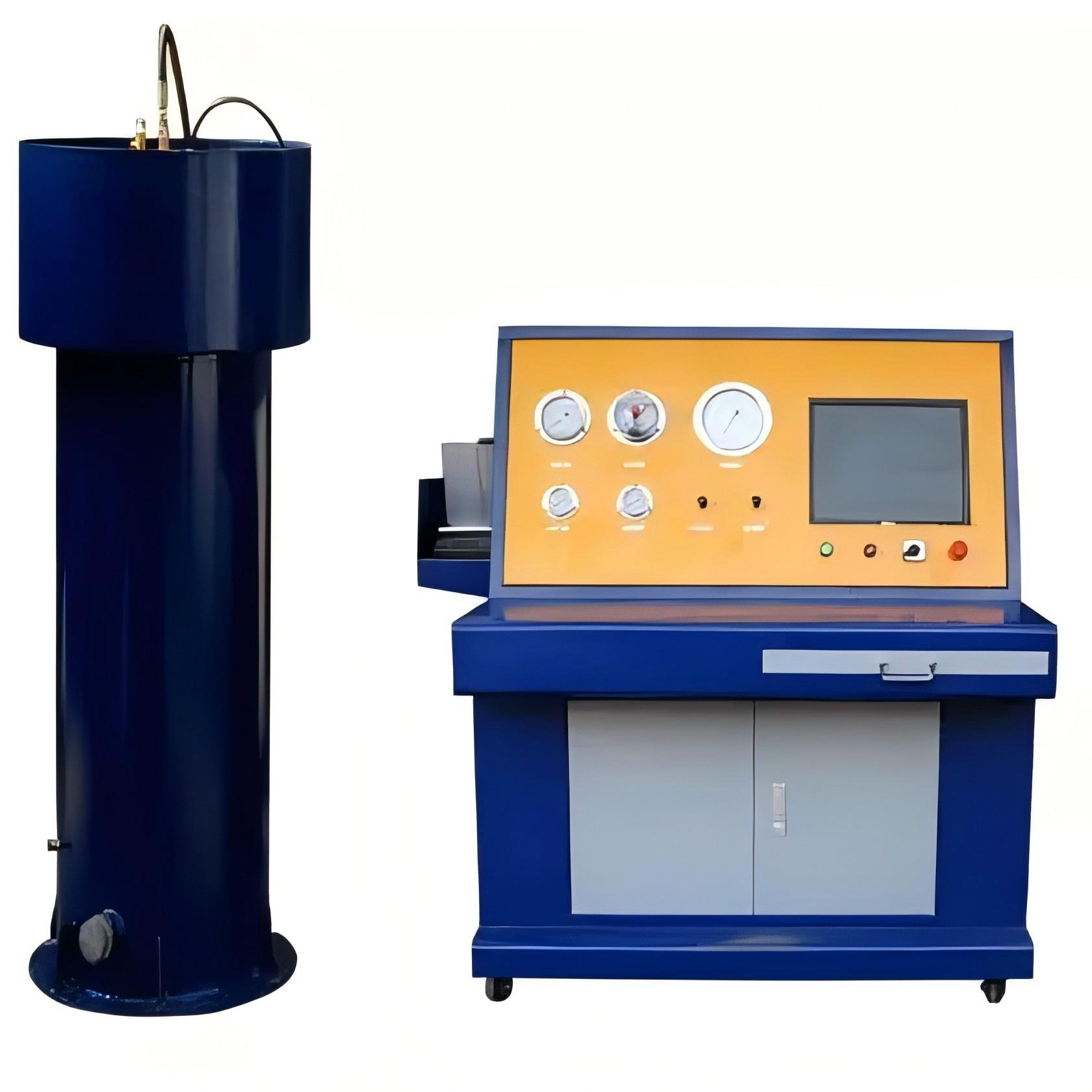
Permanent Expansion Testing Machine
Our Certification
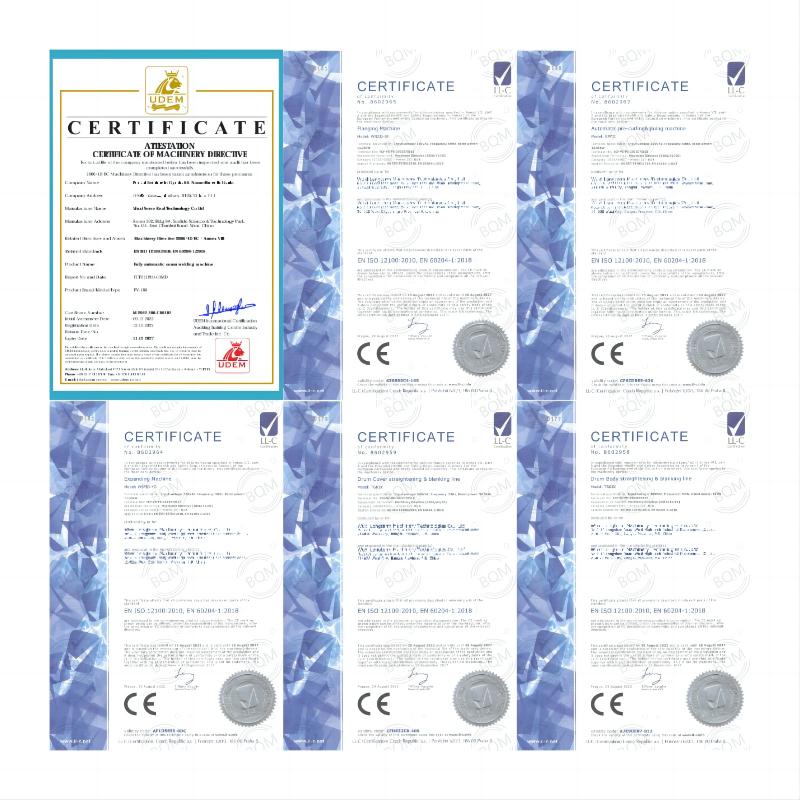
FAQ
Headquartered in CHANGZHOU, China, THLPG has served the domestic market (65.00%), Southeast Asia (15.00%), Eastern Europe (10.00%), and South Asia (10.00%) since 1995. Now THLPG has the full technology and manufacturing capability for LPG Cylinder and Propane Tank Production Line, Electric and Solar Water Heater Production Line, Pressure Vessel and Auto-gas Tank Production Line, Beer Keg and Beverage Keg Production Line, LPG Cylinder and Other Old Containers Reconditioning Plant and other container testing and refurbishment machinery.
Pre-production samples before mass production;
Final inspection before shipment (SGS, CE, UL, CSA, ISO certification available);
Accept inspection by third-party agencies or customers before shipment.
All types of LPG Cylinder and Propane Tank Production Line, Electric and Solar Water Heater Production Line, Pressure Vessel and Auto-gas Tank Production Line, Beer Keg and Beverage Keg Production Line, LPG Cylinder and Other Old Containers Reconditioning Plant and other container testing and refurbishment machinery.
Accepted delivery terms: FOB, CFR, CIF, EXW, CIP, FCA, DDU, DDP, DAP, Express;
Accepted payment currencies: USD, PHP, EUR, JPY, CAD, AUD, HKD, GBP, RMB, CHF;
Accepted payment types: T/T, L/C, MoneyGram, PayPal, Western Union;
For each project, we could provide the design service since the beginning to help build the most cost efficient and suitable plant for customers. And the service will continue after the plant is well built. Engineers will stay for a period of time after the production line is installed to ensure that the production line runs smoothly. And the training for customer’s engineers is free of charge.
Please feel free to Contact Us!
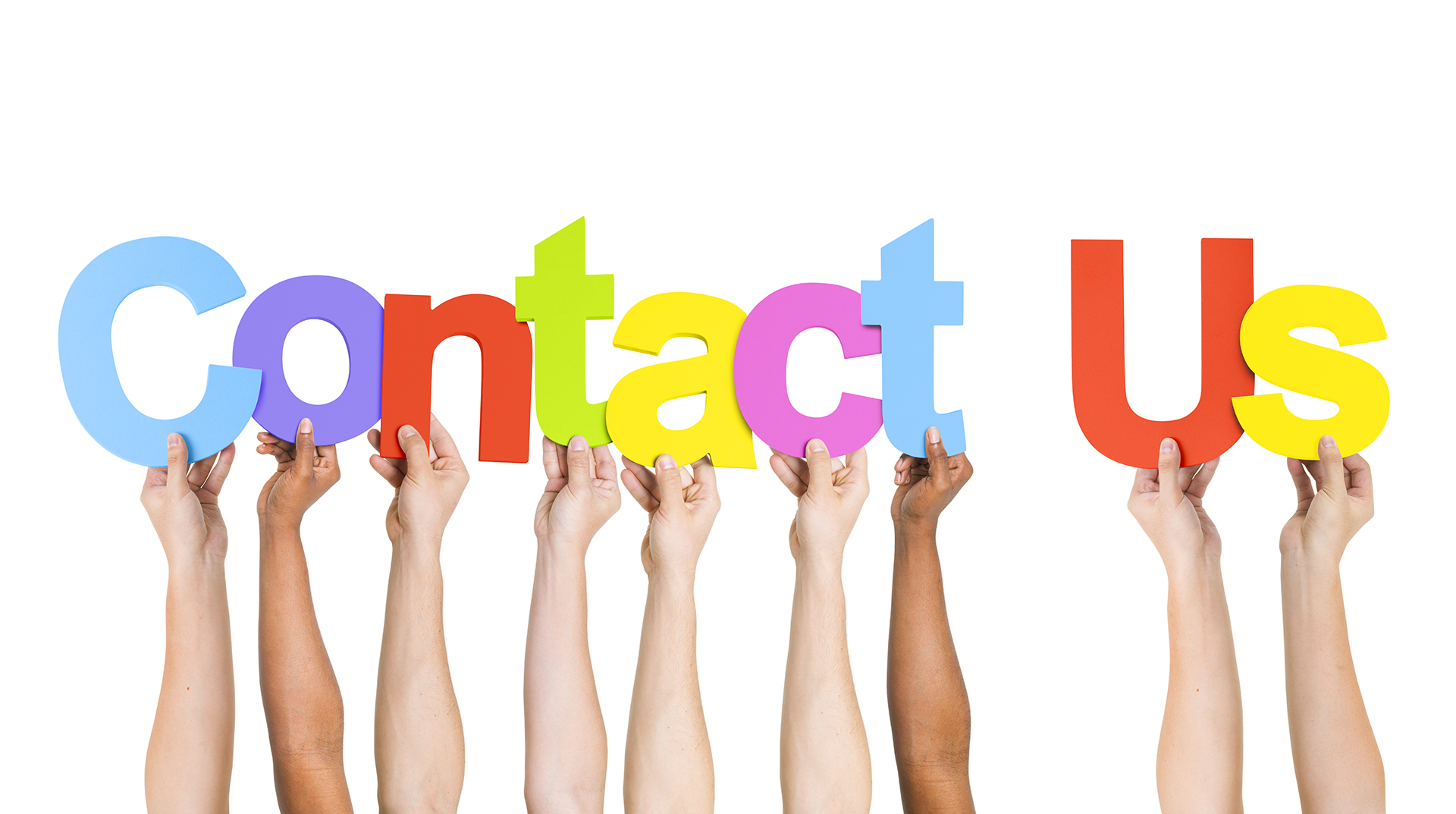